Batching plant 90 m3 jam automatic control
Concrete batching plant 90 m3 jam is an indispensable production equipment in infrastructure construction, and it is also a complex control system composed of many links. In the production of concrete, the weighing accuracy of batching, the construction proportion of batching, the moisture content of raw materials and water supply directly affect the quality of concrete. In addition, in the control system, the connection with hardware equipment, the storage of formula data, the registration of raw materials in the production process, the warehouse management, the login record of operators, the product transportation record and other aspects of management will also be able to It directly affects the production efficiency of concrete batching plant.
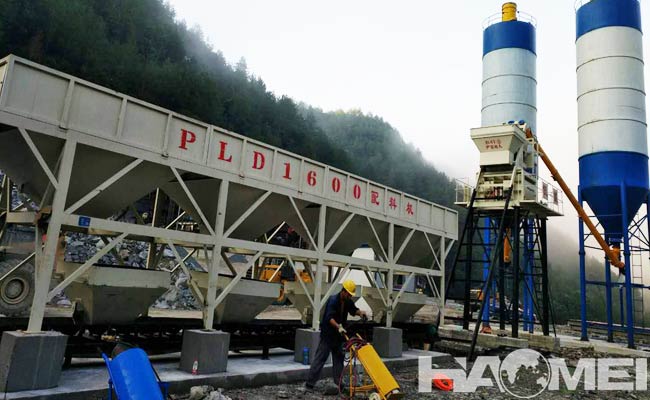
The concrete production process of concrete batching plant 90m3/h mainly consists of four parts: material bin, material scale, aggregate hopper and mixer. The material bin and material scale are the batching system, which is responsible for the accurate delivery of raw materials according to the values set in the formula. The aggregate hopper and concrete mixer are the mixing system of batching plant 90m3/h, which is responsible for concrete mixing and discharging.
The automatic control system of concrete batching plant 90 m3 jam can realize accurate and continuous control of each link in the concrete production process. First, the material bin automatically puts the material on the material scale according to the batching value set in the formula, and the system automatically stops discharging according to the weight value collected by the material scale. When the material scale discharges the material to the aggregate hopper, it also automatically stops discharging according to the weight value collected by the conveyor belt electronic scale, so as to ensure the accuracy of the batching quantity twice. At the same time, the system of batching plant 90 m3 jam adopts the method of on-line calculation of the impulse, and adjusts the impulse size in real time according to the actual situation, further ensuring the accuracy of the burden. According to the actual value and the set value, the excess material will be left on the material scale and participate in the next batch. Start to calculate the mixing timing after all feeding is completed, and inform the production completion by the electric bell.